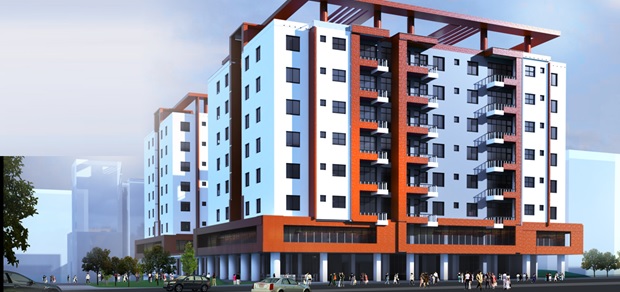
As Ethiopia’s construction industry continues to expand, sector experts and officials stress the urgent need to integrate advanced technologies and local innovations to enhance efficiency, reduce costs, and meet the country’s growing infrastructure demand.
According to the Ministry of Urban and Infrastructure (MoUI) State Minister Yetmgeta Asrat, construction accounts for 20% of Ethiopia’s GDP and over 10% of total employment. Despite its substantial economic impact, the sector still faces critical challenges, including reliance on traditional practices, poor project completion rates, and high costs for imported materials.
“While Ethiopia has a rich history in construction, the sector has not evolved in tandem with its legacy,” Yetmgeta told The Ethiopian Herald. “Technology and research are not just optional—they are essential for bridging performance gaps and achieving national development goals.”
The Construction Management Institute (CMI), a government body under the Ministry, is leading initiatives to modernize the sector. CMI Director General Eng. Tamirat Mulu noted that although there have been encouraging improvements in project delivery and quality in recent years, ongoing issues such as material shortages and dependency on imports still hinder sectoral growth.
To counteract these problems, CMI is prioritizing technology integration, capacity building, and the promotion of local material use. The institute has trained over 21,000 professionals through its Project Management Professional (PMP) programs and has introduced the “Building Information Modeling” (BIM) platform to digitize the construction process, aligning it with international best practices.
CMI also supports the enforcement of construction standards and works closely with federal and local authorities to promote environmentally friendly and inclusive building designs, including accommodations for persons with disabilities. The institute aims to increase domestic sourcing of construction inputs to 80% within the next decade.
Supporting these ambitions, Addis Ababa Science and Technology University (AASTU) is collaborating with CMI on research projects aimed at import substitution. AASTU’s Biotechnology Department Head Mesfin Tafesse explained that the university is piloting innovative solutions such as producing cement-free construction blocks using bacterial fermentation of soil.
“Due to population growth and rapid urbanization, demand for housing is soaring,” Mesfin said. “We need to combine research, technology, and public-private collaboration to develop sustainable, locally sourced solutions.”
Despite promising innovations, Mesfin acknowledged challenges in securing sufficient investment for scaling up production. However, he remains optimistic about the future impact of science-driven approaches in reducing construction costs and increasing housing supply.
Private actors are also contributing to the sector’s modernization. Architect Samson Hailgebrail, who worked in Canada’s construction industry for over 15 years, is applying his experience in Ethiopia. His team has already constructed homes using 92% locally sourced materials and is currently building five houses per month in Kombolcha, Amhara state. Using modular construction methods, Samson estimates that nearly 20 homes can be built in a single month.
“In North America, this system has existed for over 150 years,” Samson said. “In Ethiopia, the housing deficit is huge. Only 25% of the population has access to adequate housing. To meet demand, we need to build at least 500,000 homes annually. The only way to do that is through innovation and scale.”
Experts agree that unless Ethiopia embraces technological change, the construction sector will continue to lag behind demand. But with targeted investment, strong institutional support, and a shift toward modern practices, the industry has the potential to become a key pillar of Ethiopia’s economic transformation.
BY MESERET BEHAILU
THE ETHIOPIAN HERALD WEDNESDAY 2 JULY 2025