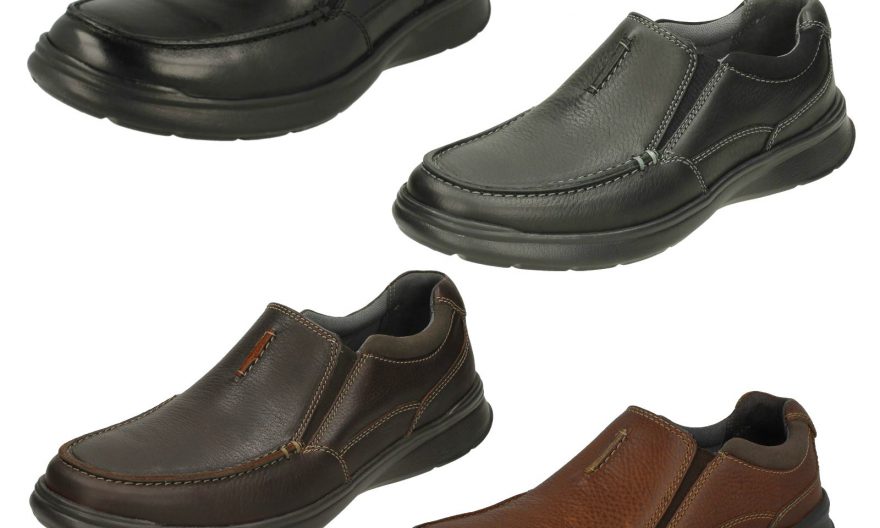
The production of leather shoes in Ethiopia dates from the late 1930s when Armenian merchants founded two shoe factories in Addis Ababa. These factories nurtured a number of shoemakers, who opened their own factories in Addis Ababa and trained their workers. Today, the neighborhood of Mercato, a huge marketplace in the city, swarms with shoemakers, wholesale shops dealing in leather, soles, and shoe accessories, and shoe retail stores.
Industrial clusters like this are ubiquitous in developing as well as developed countries because of agglomeration economies originally pointed out by Marshall (1920). If transacting parties are located near each other, transport costs are saved, transaction costs due to imperfect information and imperfect contract enforcement are lowered, and good products and superior production practices diffuse quickly. Thus, industrial clusters enhance the division and specialization of labor among enterprises, the development of the market for skilled workers, and the dissemination of technical and managerial knowledge. Such agglomeration economies attract new enterprises to a cluster, making the cluster larger and reinforcing the agglomeration economies.
The footwear industry in Ethiopia is thriving, and in the early 2000s, it managed to recover the domestic market which had been swept by imported Chinese shoes in the late 1990s. Using primary enterprise-level data, this article finds that the industry has been growing not only because of a number of new entrants but also because existing enterprises have been expanding by improving product quality and developing new marketing systems. Such multifaceted improvements have been introduced by highly educated entrepreneurs, who have successfully expanded the size of their enterprises. This development pattern is surprisingly similar to that commonly found in East Asia.
Accordingly, one of the major contributors to foreign exchange earnings and boosting the country’s economy is the shoe factory. However, the export and import of footwear depends solely on a handful of manufacturers. According to the data obtained from Leather Industry Development Institute, there are four major shoe manufacturers and exporters.
According to Tesfaye Berhanu, Director of Planning, Monitoring and Evaluation at the Institute, they are Huajayan, a large Chinese company, Yugang, a sister company, Georisha Factory, a Taiwanese company, and New Wing, an Italian company.
Earlier to the outbreak of COVID-19, these four factories alone could able to earn 70 percent of the annual market share plan for the last year. Huajayan’s sister factory, Yugang Factory, and Taiwan’s Georgesha alone generated 65 percent of their annual foreign exchange earnings up to November last year.
However, this year, especially since the outbreak of COVIDE 19 in March last year, the sector’s revenue has declined significantly. For example, it was planned to earn 50.93 million USD from the shoe market during the last eight months. Its revenue for the first eight months, however, was 26.16 million USD which is 52 percent of the plan.
According to the director, the plan certainly took into account the global and national market conditions of the field. In this regard, it was hoped that in the first six months of the 2020/21 fiscal year, COVID 19 would be reduced and the larger shoe factories, such as Huajayan, would be operational. Last year’s performance up to November has been good, but since March this year, production orders have been declining due to the threat of the COVID 19 epidemic. Some of the giant shoe manufacturers and exporters have even dispersed their workers.
Of course, the global market is in full swing. But the factories could not enter into production and export. As a result, only 52 percent of the target was achieved in eight months. Although COVID’s impact on the recession was huge, he said there were many other problems in the field.
Some of the problems are structural problems that can be solved over time. Some of them of course, need to be resolved quickly, but sustained being a problem until now because of structural problem in the field. He further explained that the sector’s biggest problem is the supply of foreign exchange.
For the past eight or nine months, there has been no foreign exchange supply for chemicals, leather goods and softeners. In this regard, some shoe factories have failed to supply the type of product that the market requires. Besides, lack of operating fund is one of the problems the factories encountered. The government is making efforts to address these issues prioritizing the manufacturing industry this year, especially in terms of foreign exchange supply.
Another problem in the past eight months has been lack of supply and exchange of salt which is domestic product and does not require foreign exchange. Salt, one of the basic inputs, is used to soften and tan the skin to make shoes.
Salt is needed not only by factories but also by skin collectors. Due to unavailability of the salt, in recent months, the skin collectors have found it difficult to collect the skins and treat with salt. However, as was often the case, there was a shortage of salt in the field for various reasons. This has been a major obstacle to the production and export of footwear.
However, the government has now solved the problem in collaboration with the Afar State. According to the director, on the other hand, the shortage of lime remains still unresolved in the field. The Derba Cement Factory, which supplies lime chemicals, has been plagued by problems with the power supply and processing of lime.
However, this problem has been resolved well since last February. But it is undeniable that it has had an impact on the industry to some extent. Tesfaye also said that the government is paying attention to the lime supply and it is not expected to be a problem anymore.
BY BACHA ZEWDIE
The Ethiopia Herald May 14/2021